Megawatt Charging System (MCS)
Introducing the Megawatt Charging System (MCS): A Game-Changer for Electric Transportation
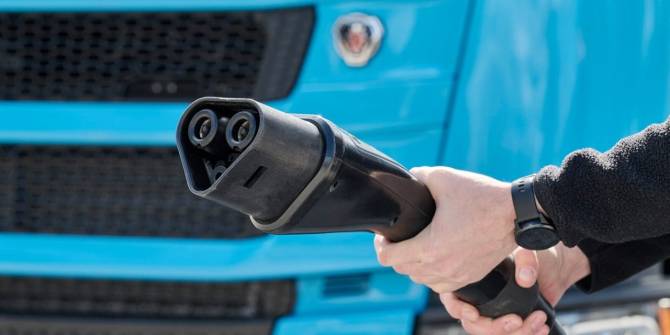
As the world increasingly turns towards electric vehicles (EVs) as a sustainable solution to combat climate change, one critical challenge persists: charging infrastructure that can keep pace with the demands of heavy-duty transport. Enter the Megawatt Charging System (MCS), a revolutionary development poised to transform how electric trucks, buses, and other large vehicles recharge.
Why Was the Megawatt Charging System Developed?
The MCS was developed to address a specific need in the electric vehicle industry—fast, efficient, and high-capacity charging solutions for heavy-duty vehicles. Unlike passenger EVs, commercial and industrial vehicles such as HGVs, buses, and large vans require significantly more power to operate efficiently over long distances. Traditional charging systems are not equipped to handle such high demands within acceptable charging times, which has been a barrier to the adoption of electric vehicles in commercial transport.
The development of MCS aims to reduce charging time dramatically, making it feasible for heavy-duty electric vehicles (EVs) to recharge in roughly the same time it takes to refuel diesel vehicles. This is crucial for maintaining operational efficiency in commercial transport, where time spent charging directly impacts productivity.
Who Developed the Megawatt Charging System?
The Megawatt Charging System is the product of collaborative efforts spearheaded by CharIN (Charging Interface Initiative), an industry association with members from various sectors including automotive manufacturers, charging infrastructure providers, and technology firms. CharIN focuses on promoting scalable and interoperable charging solutions, like the Combined Charging System (CCS) standards used widely across North America and Europe.
Key stakeholders in the development of the MCS include global automotive leaders and energy companies dedicated to establishing a standardized charging infrastructure that can facilitate the wide-scale adoption of electric heavy-duty vehicles.
What is the Intended Use of the Megawatt Charging System?
The primary use of the MCS will be for charging commercial electric vehicles that require high power to ensure minimal downtime and maximum efficiency. This includes electric HGVs, buses, and potentially, in the future, industrial and construction vehicles that can benefit from rapid recharging capabilities.
The deployment of MCS will likely be concentrated in strategic locations such as depots, logistic centers, and along major transportation corridors to allow for seamless operation of electric fleets over extensive networks.
The Ampacity of Connected Equipment
Ampacity, or the maximum amount of electric current a conductor or device can carry before sustaining immediate or progressive deterioration, is a key technical aspect of the MCS. The system is designed to deliver up to 3,000 amps at a high voltage level, which can facilitate charging powers above 1 megawatt (MW). This high capacity is instrumental in enabling the quick recharge times necessary for the effective operation of heavy-duty electric vehicles.
The MCS is rated for the highest charging rate of 3.75 megawatts (3,000 amps at 1,250 volts direct current (DC).
This capability represents a significant technological advancement over existing charging systems, which typically operate at much lower capacities. By pushing the boundaries of what current EV charging infrastructure can provide, MCS sets the stage for a future where electric heavy-duty transport is both practical and prevalent.
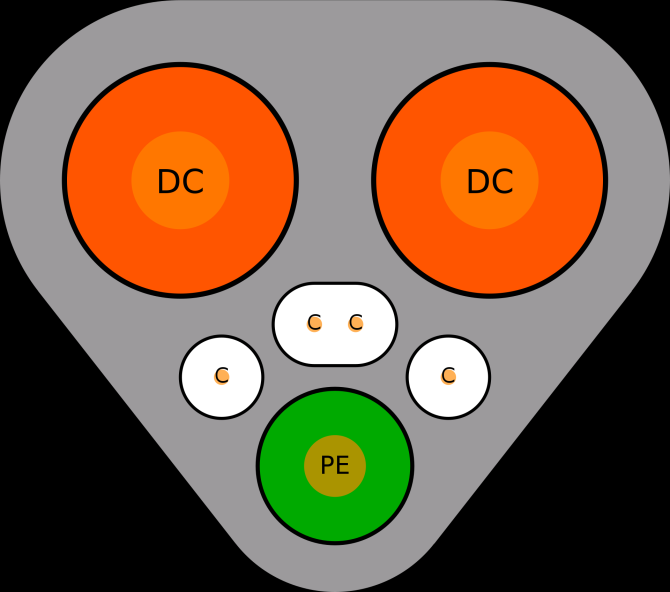
Design Requirements
The design requirements of the MCS are as follows :
- Single conductive plug
- Maximum of 1250 V DC and 3000 A[2]
- PLC + ISO/IEC 15118 (ISO 15118-20 Communication Protocols allows bi-directional energy flow for vehicle-to-grid (V2G), Smart Charging, Encrypted Communication, Plug ‘n Charge, Automated Charging)
- Touch Safe (UL2251)
- On-handle software-interpreted override switch
- Adherence to OSHA / ADA (or local equivalent) standards (dictates sizes using anthropometric data and masses using ergonomic data)
- FCC Class A EMI (or local equivalent)
- Located on driver’s side of the vehicle, hip height (ergonomics)
- Capable of being automated
- UL / NRTL certified
- Cyber-Secure
- V2X (bi-directional)
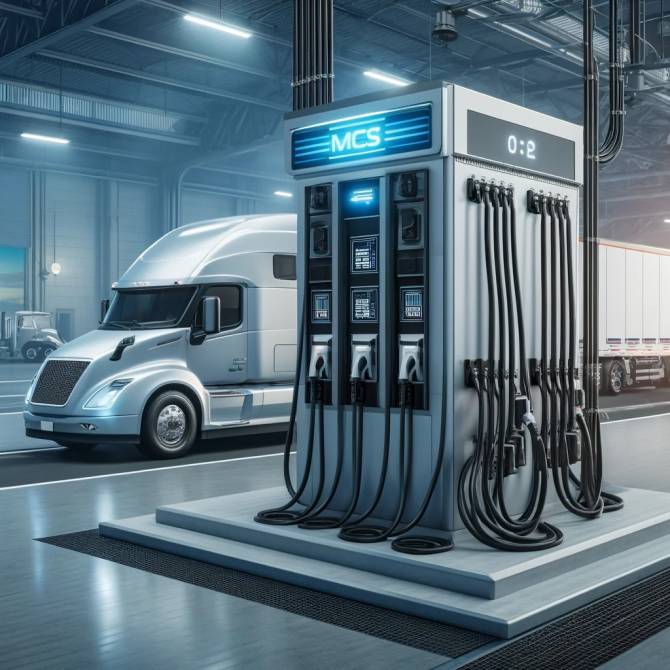